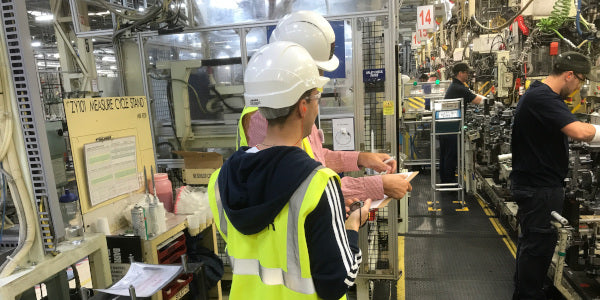
Overview
Standardisation and Kaizen are the platform that supports the Toyota Production System. Without clear standards it is impossible for people to judge if a situation is normal or abnormal. In this situation how can we ever be certain our actions are adding value to a process and not just creating more waste?
Standardised work is a tool that can be applied to any process where human interaction is present and when used correctly will lead to increased levels of motivation by creating employee process ownership and engaging them in continuous improvement activities.
Key Study Areas
- Correctly study the worksite and visualise the current state.
- Identify waste, value added and non-value added activities.
- Redesign the worksite to ensure Safety, Quality and Productivity
- Create a Kaizen plan to eliminate waste.
Aimed At
All levels up to and including Managers
Course Information
This course can be undertaken at either our Deeside Engine Plant, Burnaston Car Plant or at a client's site. There is one day of classroom based activity during which you will learn the theory and apply it to an operation simulated with Lego.
We recommend that this is combined with at least one additional day during which a real process can be studied. Holding the course at your own site will allow you to select a process of your own and generate a kaizen plan which will deliver real results.
Customer Comments
"A thorough evaluation of of our process yielded an honest appraisal of our current condition. Thanks for giving us a clear direction and showing us what is truly possible. What I have learnt is that much more detail is required than we ever dreamed."
Course Etiquette
Courses can contain participants from several organisations. Conduct should be professional to ensure that all participants are able to enjoy the course.